Square, rectangular or flat wire can be produced with a variety of standard edge conditions. Equally, wire can be produced with special edge conditions. The edge conditions are usually defined as a “radius” or a “radius of curvature.” The actual measurement of this specified parameter is dependent on the edge and finish wire shape. (ASTM B250.)
Corner Radius and Crown Edge Radius
A corner radius (below, left) is defined as any configuration between a radius and chamfer. The measurement of a corner radius is the distance from the blend point on one surface to the extension of the other surface. The established level of corner radius measurement accuracy requires that the measured value be rounded to the nearest .0005″ (.0127 mm).
A crown radius (below, right) is a round edge of a specified radius of curvature rolled into the edge of the wire. The crown radius can be rolled into any or all sides of the wire.
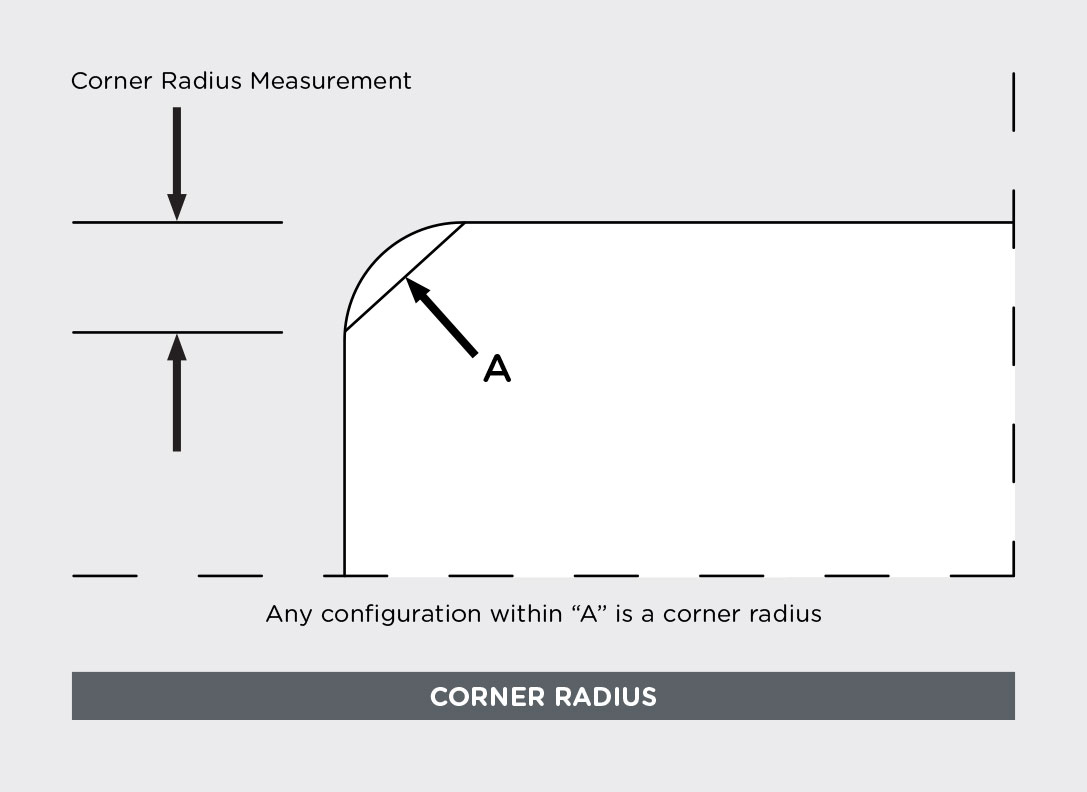
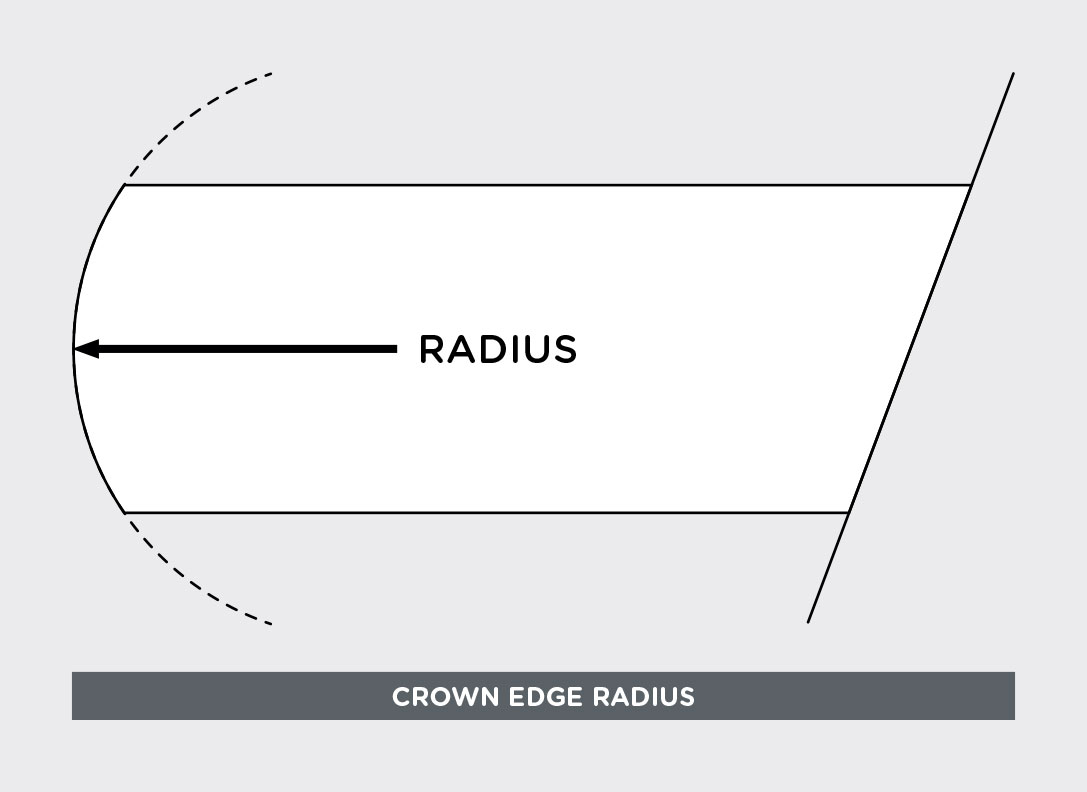
Natural Round Edge and Square Edge
A naturally-rounded edge (below, left) is formed when wire is rolled flat in a rolling mill. The natural rounded edge is not a perfect arc radius but can be approximated by a radius which is greater than half the thickness of the wire.
A square edge (below, right) is where the edge of the wire has been rolled flat to be square to the width of the material. Squared-edge flat wire will have a corner radius dimension that can be specified. Squared-edge flat wire generally accords tighter tolerances on the width dimension as compared to a natural edge.
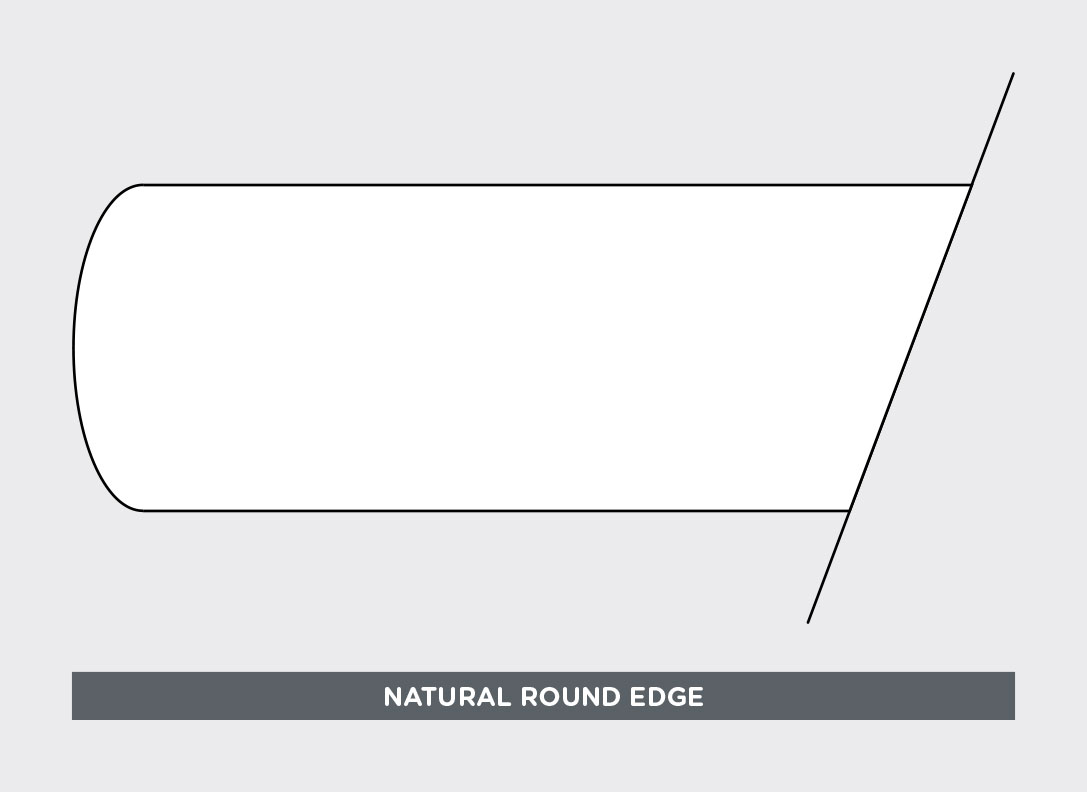
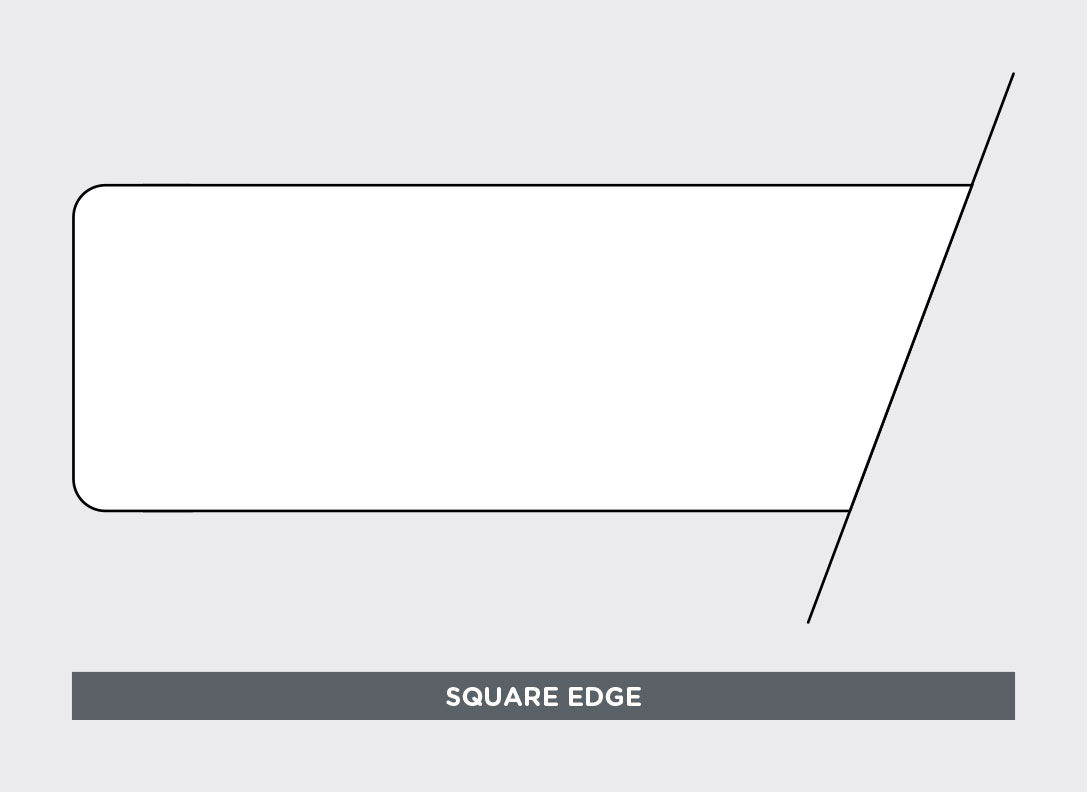